ENERGY PERFORMANCE
Insulation And Solid Timber Buildings
People often ask about the “R value” of solid timber homes, wondering if they will be warm to live in. What we really need to address is “energy performance”, or how heat passes through the “exterior envelope” (walls, roof, foundation, floor). Energy performance is a result of conduction, convection, storage, and radiation, acting in and around the exterior envelope. There are two measures of energy performance: the amount of fuel burned per unit of time at different temperatures, and the sensory “feel” of a house as it is lived in.
In practical terms, it boils down to conduction, air leakage, and heat storage.
- Conduction is the transfer of heat directly through the wall, which can be slowed down by resistance (i.e. “Rvalue” or insulation), and by storage.
- Air leakage can cause up to 30% of heat transmission even in an insulated building (e.g., a “drafty” house). This can be reduced or eliminated by caulking and sealing.
- Heat storage is a property of solid materials like wood, brick, and stone. Solid timber has a property mostly absent in conventional “stick-frame” buildings: thermal mass (the ability of wood to absorb, store, and re-radiate heat back into the house over time).
Massive timbers or logs are famous for yielding a warmth and a thermally comfortable living space that cannot be duplicated by stick-built, highly insulated structures which have little thermal mass. I know this personally from my own home north of Whitehorse, Yukon (10″ thick timbers). At -40 outside, the house “feels” warmer inside than the thermostat setting. Conventional houses don’t do this.
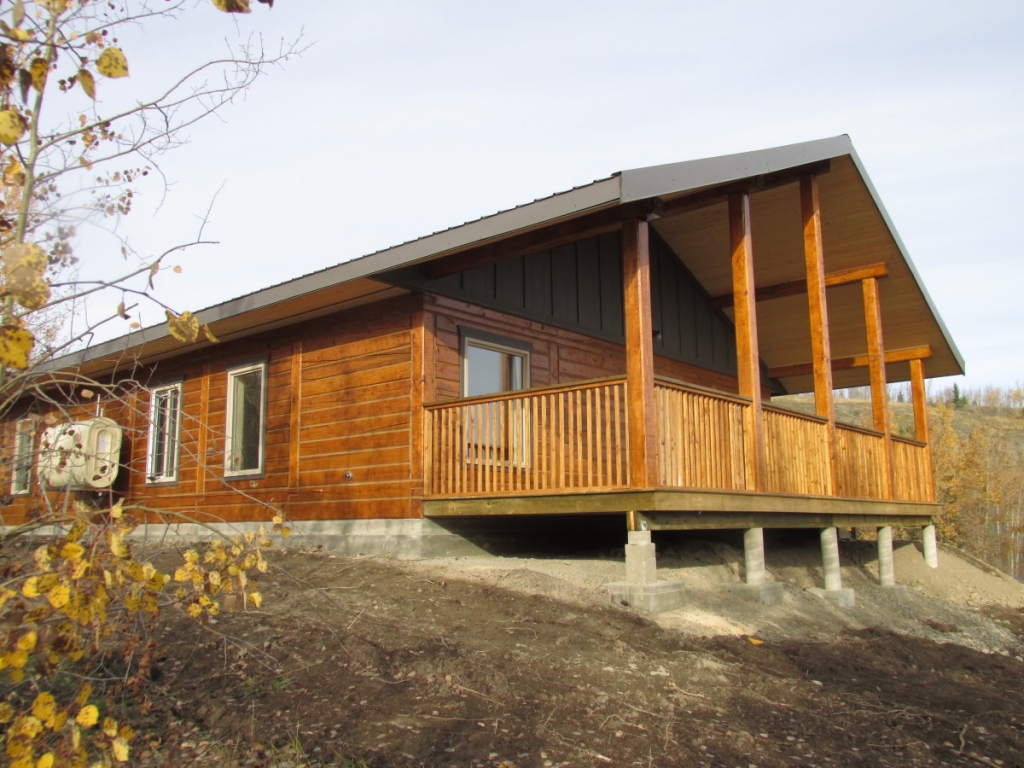
How can this be? It has to do with the thermal mass of the timbers. Stick built houses have no thermal mass to speak of, so their apparent warmth comes completely from R value (insulation) and minimal air leakage. A well-built timber house pays attention to both of these, of course, but it also has considerable thermal mass to add to the factors that determine energy performance. The thermal mass of solid wood acts as an energy buffer – heat is continually radiated into the house from the timber walls with the result that the entire house is a radiant heater. It heats also by conduction: back up against a timber wall on a cold winter day and you will feel warmth – a conventionally insulated house wall will feel cool. Voila: the manifestly greater feel of comfort in a good timber house: you are surrounded by radiant heat.
There is much confusion about this because of the almost universal use of “R value” as a measure of how well a structure will retain heat. At some point, somebody calculated that 1″ of a typical softwood had an R-value of about 1.4 or so. By this measure, an 8″ timber building has an R-value of 11.2. Since an 8″ fiberglass-insulated stud wall has an R-value of about 29, you would expect the log house to be a very cold structure indeed.
But this is not the experience of generations of people in North America and Scandinavia who grew up in timber buildings and stayed warm and comfortable. Theoretically calculated R-value ratings are not lining up with actual experience. It is not that R-value is invalid – but that it is not the full story. R-value measures resistance to heat loss through transfer, while thermal mass measures capacity to store heat. Both are important to understanding energy performance, or how much energy a house consumes to keep a constant temperature. The third factor is air flow, or draftiness. The tighter a building the better. Good caulking on dry timber: the secret to air-tightness in a Heartland Timber Home.
The building authorities and conventional builders stick to R value (thermal resistance) as the sole measure of thermal performance and have organized Building Codes around this.
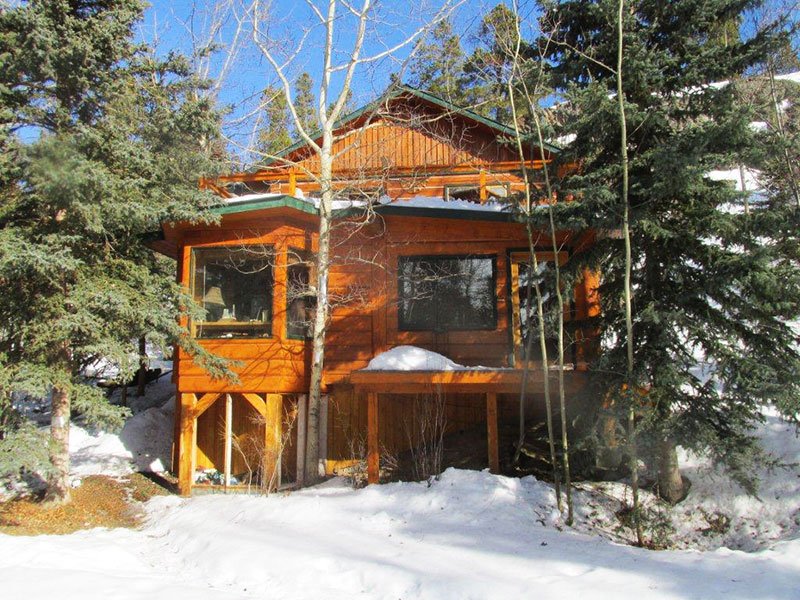
To meet contemporary codes, log and timber builders have two courses of action:
1. Increase the energy efficiency of other building components (roof, floor, foundations, windows, heaters, HVAC, etc.). For example, a unit increase in roof insulation is more effective than the same unit applied to walls. Heartland Timber Homes meets modern codes by adopting all of these strategies into its designs.
2. Add supplemental insulation to the walls. HTH does this too in extreme situations. We add a cladding of high R-value foamboard to the outside of the timberframe shell, and then clad it with milled siding that replicates the timberframe appearance. The result is an unique hybrid system: an R30 wall that has full thermal mass and all the structural and aesthetic benefits of timberframe. We use this approach in extremely cold places where the client requests it, or where the local code requires a high R-value wall, such as in Whitehorse. (Whitehorse requires R-28 walls; outside of town the National Code stipulates less). Cold climate housing researchers in Alaska consider our “Arctic Insulation Package” to have hit the perfect balance between using low-impact sustainable materials, healthy living environment, and energy performance.
But there is another way to meet building codes. Create “insulated logs” that are essentially foam blocks with a veneer of wood – no thermal mass benefits, no structural integrity of solid wood. Other than the pretense of a faux “log cabin” look, I fail to see any utility of this approach. You can do a better R-value with stick built if that is your main objective. If you like the structural integrity, engineering strength and durability, winter warmth and snugness of solid timbers, stick with the real thing.
Want to read more?
Check out: Energy Performance of Log Homes
As noted in the 12/2/13 Environmental Building News article “Buffering Humidity with Interior Finishes”, the attention to building dynamics is even more important as our buildings get tighter. “Just as thermal mass can be used in passive design to redistribute heat, it is possible to use certain interior finishes to redistribute moisture – a strategy known as moisture buffering or humidity buffering.”